

The images above show a great example of the difference between the two wet sanding methods. Personally I like using the 3m step 1 compound with a rotary buffer to start, followed by a Rupes blue WOOL pad, finishing of by the Rupes Yellow foam glazing pad. Once we have completed the sanding stage its time to buff. Think of it like body filler, we wouldn't start blocking filler with 320 or 400 so why would we start blocking clear with 1200-1500g? Class Location: N11016 US HWY 45 Birnamwood, WI 54414 Dates: December 5th,6th,7th,8th Class Details: 4 day hands on restoration class with Freddy Carlson, Colten Davidson and Jason Kilmer. Having applied 4 coats of clear in one spray we ensure that we have enough mil thickness to affectively block our clear straight and the reason we must start aggressiveis to get the clear truly straight. Using just 3000g on a DA will ruin the super flat finish you've been trying to achieve. The typical steps when wet sanding with a foam block are 800g, 1200g,1500g, 2000g and 3000g progressively all done by hand. What we DO NOT want to be sanding on a "rubber ball". To get a super straight finish we want our clear fully cured and hard from the bottom up.
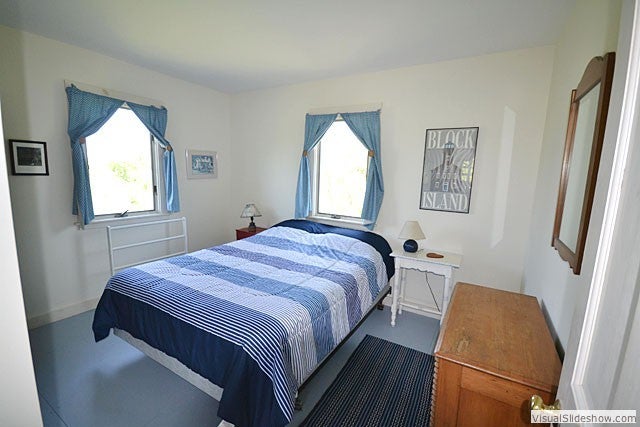
Preferably I will let the clear dry overnight then bake it with an infrared light, at a metal temp of 130-140 degrees F, which will bake the clear from the inside out, rather than bake the clear in the booth. A method which will safeguard you from having trapped solvents. Between the 2nd and 3rd coats 20 minute flash time and between the 3rd and 4th coats 30 minute. The reason we do 4 coats of clear at once instead of flow coating or "double clearing" is because we want adequate clear mil thickness without a recoat layer.įor example if using Global D8152 glamour clear, spraying in about 80 degrees F, I will give it ten minutes between my first and second coats. Typically when wet sanding with acrylic blocks, I will apply 4 coats of clear in one spray, allowing more flash time for each coat.
